- PhDWire
- Posts
- Silicon heterojunction back contact solar cells by laser patterning|Publishd in Nature
Silicon heterojunction back contact solar cells by laser patterning|Publishd in Nature
Lasers simplify the manufacture of back-contact solar cells and improve power conversion efficiency. This method produced the first silicon solar cell with more than 27% efficiency.
HBC Solar Cell Design
This paper outlines the key features of HBC solar cells that achieve a power conversion efficiency (PCE) of more than 27% (Figure 1a). At the device level, the overall PCE is improved by processes that reduce recombination current density and contact resistivity (Figure 1b). Silicon heterojunction technology (SHJ) passivation contacts are used, with an intrinsic/n-type amorphous silicon layer for the N contact and an intrinsic/p-type amorphous silicon layer for the P contact. The unique back-side patterning design of the back-contact (BC) cell helps reduce recombination at the boundary, enabling efficient passivation contacts, laser damage-free laser patterning, and undercut control (Figure 1b) . In addition, optimization of contact spacing and resistivity of the silicon wafer reduces electrical shading effects and improves carrier recombination and transport efficiency (Figure 1c). With these improvements, the authors achieved a highest PCE of 26.93% on a full M6 wafer, and after masking the edges, a PCE of 27.3% was obtained on a specified area of 243 cm² (Figure 1e) . External quantum efficiency (EQE) and reflectance measurements are shown in Figure 1f.

HBC High-grade passivated contacts
Here, we develop a dense passivation contact approach to address passivation and contact resistivity issues in N-contacts (Figure 2a). By depositing a hydrogen-rich porous layer (i0) and a subsequent dense layer on an oxygen-modified silicon surface, we achieve optimized passivation. High temperatures (>190°C) can accelerate the formation of SiH2 and reduce epitaxial growth, thereby improving surface passivation and conductivity (Figure 2b). In addition, increasing the temperature helps to form a denser film, improving its conductivity and resistance to laser damage (Figure 2g). The authors found that the dense layer has a relatively low hydrogen content (18%) but still maintains excellent passivation quality (Figure 2e). By adjusting the microstructure factor R* of the i0 and i1 layers, the contact resistivity is significantly reduced from 93 mΩ·cm² to 43 mΩ·cm² (Figure 2f). These results show that better passivation and conductivity can be achieved by optimizing deposition conditions and material density .

Laser Patterning
High-precision and fast laser systems can process about 15,000 wafers per hour in the photovoltaic industry, but due to laser beam induced damage (LBID), the efficiency of HBC solar cells is difficult to exceed 26%. A three-step laser patterning process (P1, P2, P3) is used to selectively remove the contact layer to achieve an N/P polarity structure (Figure 3a) , where P2 uses a single-shot mode to protect the passivation of the N contact. Pulsed green and ultraviolet picosecond lasers are used for P2 and P3, respectively, to reduce thermal effects. The appropriate laser energy density was determined through simulation and experiments to avoid damage to the passivation layer (Figure 3d). Although excessive temperatures during laser processing may cause passivation degradation, HBC cells manufactured using full laser patterning outperform photolithography technology in terms of Jsc and FF, showing higher efficiency (Figures 3f and g)
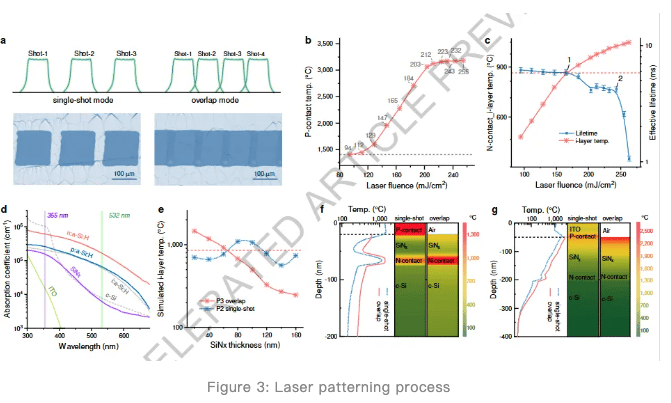
Sustainability at terawatt scale
To achieve carbon neutrality by mid-century, annual photovoltaic power generation is expected to reach 3,235 terawatts by 2032. The authors developed an ESMRC model (efficiency, scalability, manufacturability, reliability, circularity) to assess sustainability. Technologies such as PERC, TOPCon, SHJ, and HBC exhibit efficiencies of more than 25% and good circularity, but the supply of key materials such as silver and indium limits scalability (Figure 4a). The authors achieved an efficiency of 26.5% for indium-free HBC solar cells and 26.2% through copper paste metallization (Figures 4b, 4c) . HBC outperforms PERC and TOPCon in efficiency and scalability, but has a higher manufacturing complexity (Figure 4d). Through laser patterning improvements, HBC has a process time of only one-third of TOPCon and has a carbon footprint advantage (Figure 4f). The authors fabricated a 634 W HBC solar module, demonstrating that HBC technology has significant advantages in large-scale production.
