- PhDWire
- Posts
- Small: Chemical-physical synergistic assembly of MXene/CNT nanocoatings in silicone foam for reliable piezoresistive sensing in harsh environments
Small: Chemical-physical synergistic assembly of MXene/CNT nanocoatings in silicone foam for reliable piezoresistive sensing in harsh environments
Robust MXene/CNT nanocoated PDMS foam sensors offer high sensitivity, stability across temperatures (-60-210°C), and fire resistance, advancing flexible sensor technology.
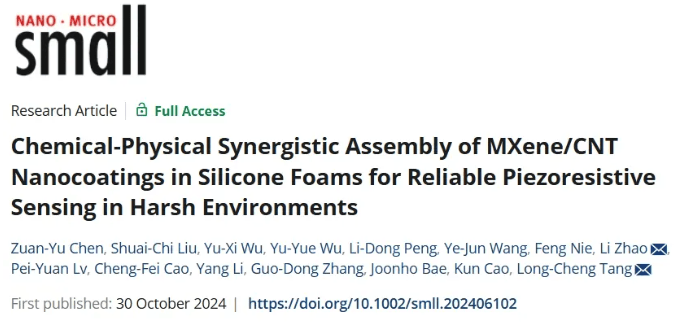
Background
Flexible polymer-based piezoresistive sensors can adapt to curved surfaces and respond to large deformations, playing a vital role in the fields of human-computer interaction, medical monitoring, and vapor/gas detection. With the development of practical application requirements, flexible pressure sensors need to output stable, highly sensitive, and reliable electrical signals for real-time detection. In contrast, the introduction of porous structures into polymer matrices provides new opportunities for flexible sensors, because the changes in conductive paths caused by skeleton deformation and mutual contact/separation of pores can lead to higher sensitivity and a wider detection range. Therefore, traditional piezoresistive sensors constructed from melamine (MA) and polyurethane (PU) foams have sprung up, which has been recognized as one of the most economical and simple strategies. However, these carbonaceous foams have poor structural strength and tend to degrade and damage under complex conditions, such as a wide temperature range (-60-210°C), acidic or alkaline environments, and organic gas environments, resulting in the loss of electrical signals. In addition, due to their inherent flammability, some of these foams often cause catastrophic fire accidents, which further hinders the applicability of flexible sensors in harsh environments.
Compared with carbonaceous foam, polydimethylsiloxane (PDMS) foam is one of the ideal substrates for fabricating high-performance piezoresistive sensors because the unique Si-O-Si chain endows PDMS polymer with excellent properties, including mechanical flexibility, hydrophobicity, environmental stability, etc. Similarly, due to its inherent electrical insulation, PDMS foam requires the construction of conductive paths by adding a large amount of conductive fillers. However, high-content particle filling increases the viscosity of the prepolymer, making the foaming process difficult and leading to the agglomeration of nanoparticles, which contradicts the development of sensors with ideal porous structure and sensing performance. Therefore, alternative methods have been devoted to improving the porous structure and sensitivity of sensors using mixed filler template method, template-assisted vapor deposition method, 3D printing method and dip coating method. Admittedly, these methods overcome the poor porous structure caused by high-content particle filling and improve the sensitivity of PDMS foam, but due to chemical inertia, strong interfacial bonding between PDMS polymer and nanoparticles has not yet been achieved. This poor interfacial bonding will definitely lead to the loss of conductive signals during long-term detection. On the other hand, integrating conducting polymers into PDMS foams, such as poly(3,4-ethylenedioxythiophene):poly(styrenesulfonic acid) (PEDOT:PSS), has been shown to be an effective strategy to address the interface issue. Nevertheless, these conducting polymers may be oxidized or degraded by chemical components in harsh environments, resulting in reduced sensitivity and conductivity. Therefore, achieving significant and reliable conductivity in silicone foams remains a major challenge. In addition, to meet the application requirements in more harsh environments, flexible polymer foam sensors need to maintain their structural integrity at high temperatures without performance degradation.
Highlights of this article
1. This work designs and characterizes a robust MXene/CNT nanocoating on the foam surface, where the chemical assembly of MXene nanosheets and the physical anchoring of CNTs lead to a strong interfacial bonding, which endows the foam with structural reliability and unexpected multifunctionality without compromising its intrinsic properties.
2. The optimized foam nanocomposites maintained excellent wide-temperature flexibility (-60-210°C) and elasticity (≈3% residual strain after 1000 cycles).
3. The nanocomposites exhibited good sensitivity in a wide stress range of 0-70% and showed remarkable stability in acidic and alkaline environments.
4. The foam with excellent fire resistance (UL-94 V-0 rating) provides stable sensing behavior (over 300 cycles) even after 5 seconds of flame exposure, making it one of the most reliable sensing materials to date.
Graphical analysis


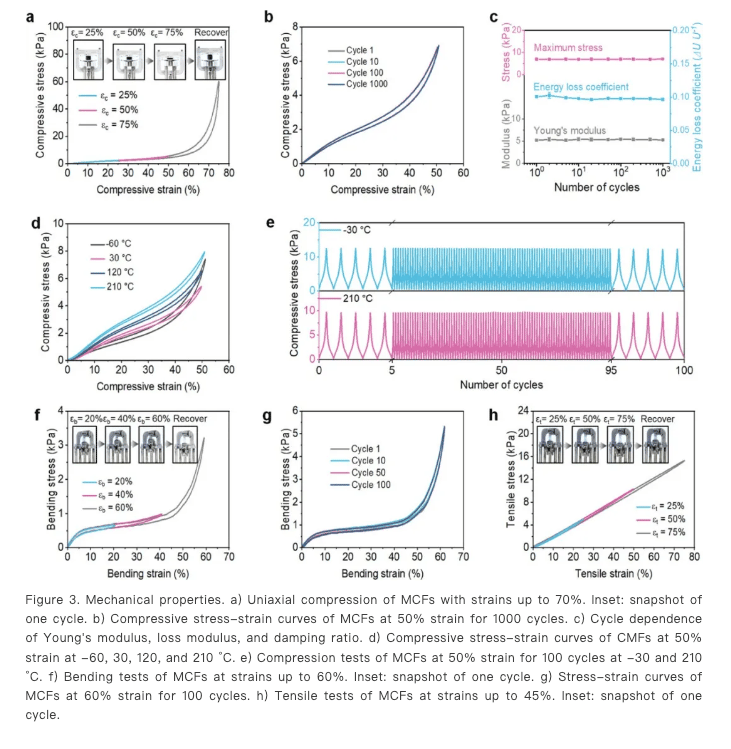


